Platform Technology
Waste-to-Energy (WTE) Incineration Process
Process Overview
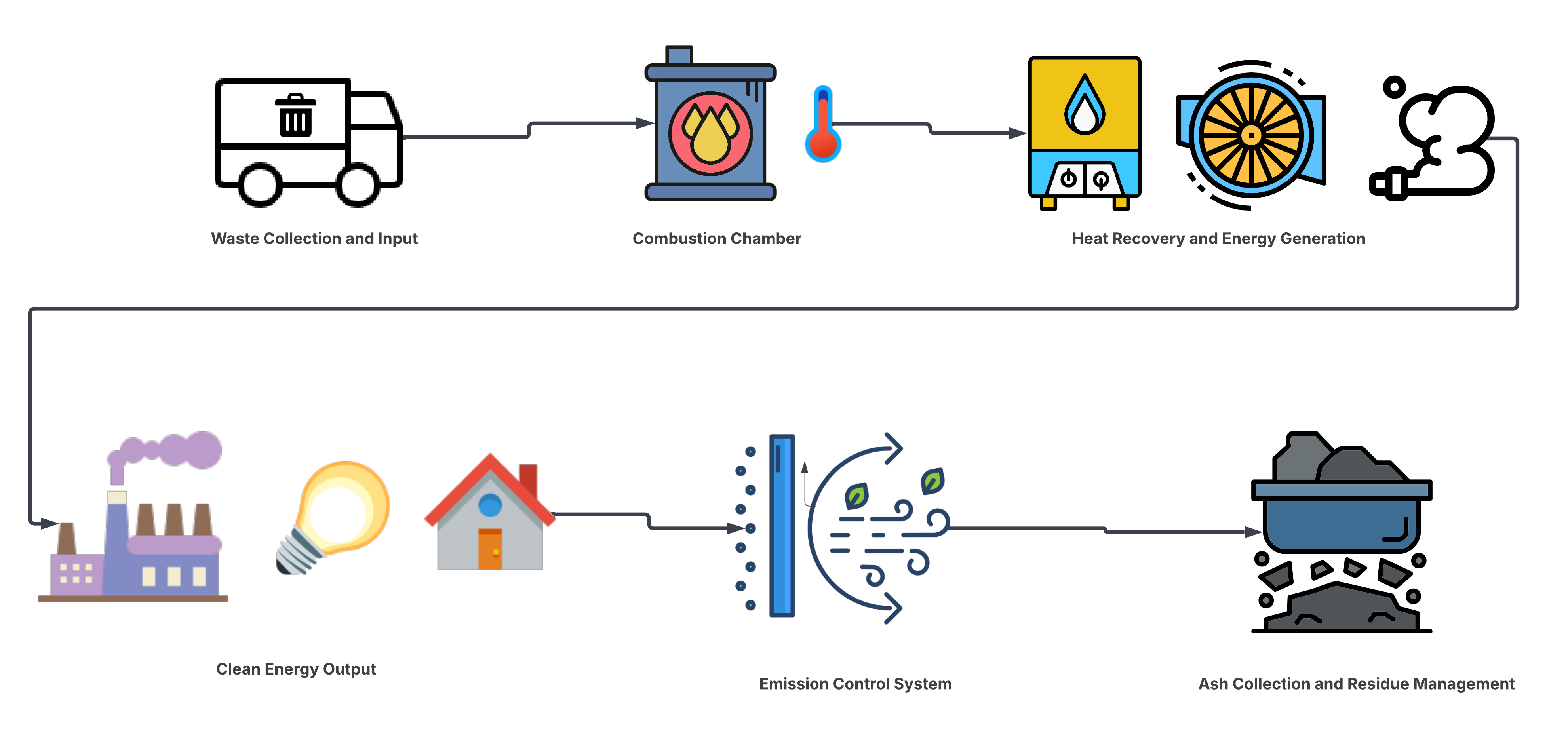
The waste-to-energy incineration process consists of several key stages, ensuring efficient energy conversion while minimizing environmental impact:
- Waste Feeding & Sorting – Municipal and industrial waste is fed into the incinerator after pre-sorting to remove recyclables and hazardous materials.
- Primary Combustion (Oxidation Chamber) – Waste is combusted at 850–1,200°C, breaking down organic matter and producing heat.
- Secondary Combustion (Post-Combustion Chamber) – Any remaining volatile gases are burned completely to minimize emissions.
- Heat Recovery (Heat Exchanger/Boiler System) – The heat generated is transferred to a heat recovery steam generator (HRSG), producing steam.
- Energy Conversion (Steam Turbine/Generator) – The steam drives a turbine, generating electricity or providing direct heating.
- Flue Gas Treatment (Emissions Control) – Exhaust gases pass through filtration systems, including scrubbers, electrostatic precipitators, and catalytic converters, to remove particulates and pollutants before being released.
- Ash Collection & Disposal – Bottom ash (non-combustible material) is collected, and fly ash (fine particulates) is captured by filtration systems. Both can be processed for construction materials or safe disposal.
Technical Specifications of Low-Volume WTE Incinerators
Outlines of key technical parameters of our low-volume waste-to-energy (WTE) incinerators, designed for small-scale applications. These incinerators efficiently convert waste into energy while minimizing environmental impact. Operating at high temperatures, they ensure complete combustion, reducing waste volume significantly. Advanced emissions control technologies are integrated to meet stringent environmental standards. The system is optimized for decentralized use, making it ideal for remote communities and commercial applications.
Waste Calorific Value & Energy Output
The energy potential of waste is determined by its calorific value (CV), which measures the amount of energy released during combustion. Different waste types have varying calorific values, influencing the efficiency and energy output of the waste-to-energy (WTE) incineration process.
High-calorific waste, such as plastics and paper, generates more energy, making it suitable for efficient power generation. However, it requires advanced emissions control systems to manage pollutants. Organic and food waste, with a lower calorific value, produces less energy but still contributes to reducing landfill methane emissions.
A typical low-volume WTE incinerator processing 1 ton of mixed municipal waste (CV ~10 MJ/kg) can generate approximately 2-5 MWh of electricity, depending on system efficiency. This energy can power local businesses, homes, or be integrated into microgrid systems for decentralized energy solutions.
Comparison: WTE Incineration vs. Landfill Gas Recovery
WTE incineration produces cleaner energy and eliminates methane emissions, while landfills continue to emit methane (25x more potent than CO₂).
Emissions Control & Filtration System
Modern WTE plants use multi-stage filtration to meet environmental standards (e.g., EU Industrial Emissions Directive, Canada CEPA regulations).
- Cyclone Separator: Removes large particulate matter.
- Acid Gas Scrubber: Neutralizes acidic pollutants (e.g., HCl, SO₂).
- Activated Carbon Injection: Absorbs heavy metals and dioxins.
- Selective Catalytic Reduction (SCR): Converts NOₓ into nitrogen and water, reducing air pollution.
Join Us on Our Journey
Ready to transform waste into energy? Contact Cleanwatt today to discover how our innovative solutions can revolutionize waste management for your community or industry. We are dedicated to providing sustainable, scalable energy solutions that exceed your expectations.
Email: contact@cleanwattsolutions.com